Durable Epoxy Boards for Various Applications: Available in Different Thicknesses
By:Admin
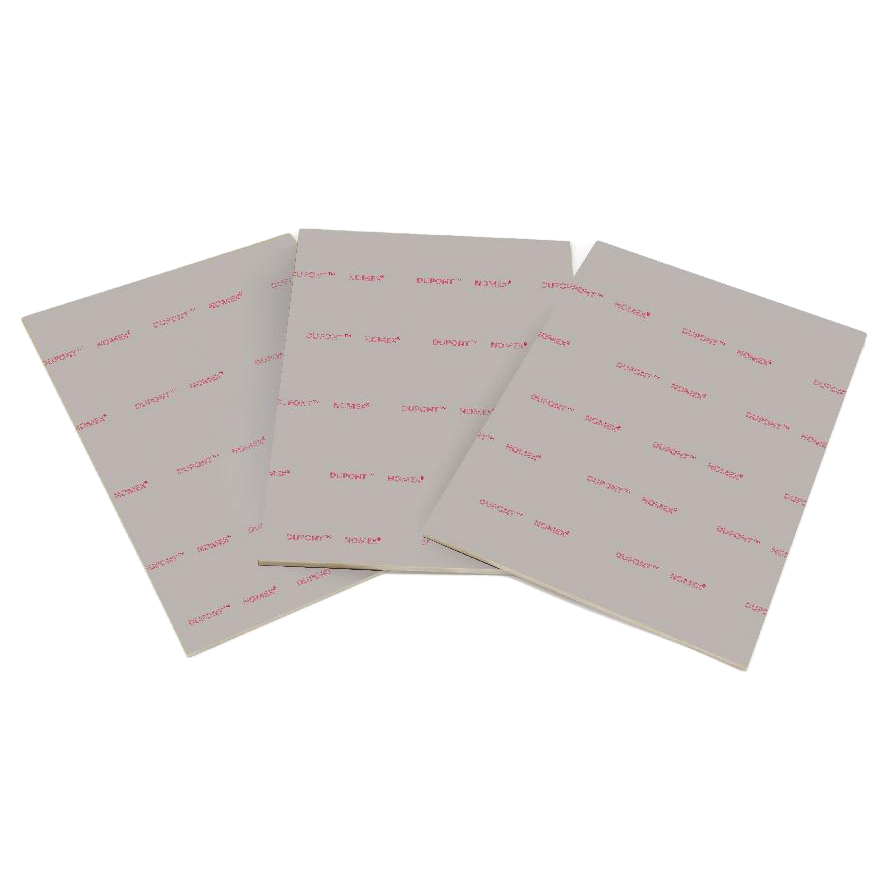
In the world of electronics and circuitry, the demand for high-quality materials and components is constantly on the rise. As technology continues to advance, manufacturers are continuously seeking new and innovative materials to meet the needs of their customers. This is where the latest innovation in epoxy board manufacturing comes into play.
One company that is leading the charge in this area is {}. With over 20 years of experience in the industry, they have built a reputation for delivering cutting-edge solutions to their customers. Their latest offering, the Different Thickness Epoxy Board, is set to revolutionize the market by providing a superior level of performance and reliability.
The Different Thickness Epoxy Board is a testament to the company's commitment to innovation and excellence. It comes in various thickness options, ranging from ultra-thin to standard thickness, catering to the diverse needs of their customers. This versatility makes it an ideal choice for a wide range of applications, from consumer electronics to industrial equipment.
One of the key features of the Different Thickness Epoxy Board is its exceptional electrical properties. It offers low dielectric loss and high insulation resistance, ensuring the smooth and efficient flow of electric currents. This makes it an ideal choice for use in high-frequency circuits, where signal integrity is of utmost importance.
In addition to its superior electrical properties, the Different Thickness Epoxy Board also boasts excellent mechanical strength. It is highly resistant to impact and has a high flexural strength, making it a reliable choice for applications that require durability and resilience.
Furthermore, the Different Thickness Epoxy Board is designed to withstand harsh environmental conditions. It is resistant to moisture, chemicals, and extreme temperatures, ensuring that it remains stable and reliable in any setting. This level of durability and resilience makes it an ideal choice for use in challenging environments, such as automotive and aerospace applications.
The company's innovative manufacturing process ensures that the Different Thickness Epoxy Board meets the highest standards of quality and consistency. Each board undergoes rigorous testing and inspection to ensure that it meets the exact specifications and requirements of the customer. This commitment to quality has earned the company a reputation for delivering products that exceed expectations.
With the introduction of the Different Thickness Epoxy Board, the company is set to further solidify its position as a leading provider of high-quality materials for the electronics industry. Their dedication to innovation and excellence is evident in every aspect of the product, from its performance to its reliability.
In conclusion, the Different Thickness Epoxy Board is a game-changer in the world of epoxy board manufacturing. Its exceptional electrical properties, mechanical strength, and environmental resilience make it a top choice for a wide range of applications. With its introduction, the company {} has once again demonstrated its commitment to delivering innovative and high-quality solutions to its customers. As technology continues to advance, the Different Thickness Epoxy Board is poised to play a pivotal role in shaping the future of electronics and circuitry.
Company News & Blog
Discover the Advantages of Prepreg Fiberglass: A Comprehensive Guide
Prepreg Fiberglass Emerges as the Ultimate Solution for Diverse IndustriesPrepreg fiberglass is an advanced material that is increasingly becoming popular in a wide range of industries, and for good reasons. From aerospace engineering to automotive manufacturing, prepreg fiberglass is seen as the ideal solution for achieving superior durability, strength, and lightweight properties in various applications. This innovative material is made by impregnating fiberglass cloth with a thermosetting resin system, which creates a reinforcement material that provides exceptional performance capabilities.One of the main advantages of prepreg fiberglass is its ability to offer high strength-to-weight ratio, far superior to metals such as steel or aluminum. This makes it an excellent choice for manufacturing lightweight structures, particularly in aerospace, automotive, marine, and sporting industries. It can be used to create parts and components that are not only lighter but also stronger, stiffer, and more resistant to impact and wear. The result is optimized performance, improved fuel efficiency, reduced costs, and greater environmental sustainability.Another notable benefit of prepreg fiberglass is its versatility. It can be tailored to meet specific requirements of various applications, from temperature resistance to flame retardancy and chemical resistance. Moreover, it can be molded into different shapes and sizes, using different fabrication methods such as compression molding, autoclave curing, vacuum bagging, and pultrusion. This means it can be used to create complex parts with intricate geometries, further expanding its range of possible uses.The use of prepreg fiberglass is not limited to industrial applications; it also has a lot of potential in architectural and design fields. Thanks to its aesthetic qualities, such as translucency, colorability, and texture, it can be used to create unique and eye-catching structures that enhance a building's visual appeal. This material has already been utilized in the construction of many landmark buildings, including the Guggenheim Museum in Bilbao, Spain, and the Beijing National Stadium, better known as the "Bird's Nest."The potential of prepreg fiberglass is not lost on innovative companies such as X, which specializes in developing and manufacturing advanced composite materials for a wide range of industries. The company's expertise lies in creating highly customized solutions to meet the specific needs of each customer. X has a wide range of prepreg fiberglass products that are suitable for different applications, from aerospace to medical equipment.One of the company's most prominent products is its high-performance prepreg fiberglass, which offers unbeatable strength, durability, and stiffness. This material has been used in the manufacture of various components of commercial aircraft such as tail cones, floor beams, and wing skins. The company's prepreg fiberglass has also found extensive use in the automotive industry, where it is employed in the manufacturing of lightweight structural parts, including suspension components, engine coverings, and chassis components.Another impressive product from X is its fire-resistant prepreg fiberglass. This material has exceptional fire-retardant properties, making it suitable for use in high-risk industries such as transportation and construction. Additionally, the company's prepreg fiberglass is compatible with various resin systems, including epoxy, phenolic, and polyester, among others, giving customers the flexibility to choose the best material for their particular needs.In conclusion, prepreg fiberglass is a highly adaptable material that offers a range of benefits to various industries. Its unique combination of properties, including high strength, lightweight, and versatility, make it an ideal solution for different applications from aerospace, automotive, marine, construction, and sporting equipment. As the use of composite materials becomes more widespread, the use of prepreg fiberglass will continue to grow, providing opportunities for innovative companies like X to create tailor-made solutions that meet the needs of a diverse range of customers.
The Ultimate Guide to G10 Material: Everything You Need to Know
G10 Material: A Strong and Durable Solution for Various ApplicationsIn the world of industrial materials, the demand for high-quality, durable, and reliable materials is ever-growing. With advancements in technology and the need for stronger and more resilient materials, companies are continuously searching for solutions that can meet these requirements. One such material that has been gaining attention in recent years is G10 material.G10 material, also known as composite laminate, is a high-pressure fiberglass laminate that is known for its exceptional strength, durability, and resistance to moisture, chemicals, and extreme temperatures. This material is commonly used in a wide range of applications, including aerospace, marine, automotive, and industrial manufacturing.One company that has been at the forefront of producing high-quality G10 material is {Company}. With over XX years of experience in the industry, {Company} has established itself as a leading manufacturer of composite materials, including G10. With state-of-the-art manufacturing facilities and a team of highly skilled engineers and technicians, {Company} has been able to produce G10 material that meets the most stringent quality standards.G10 material is composed of layers of fiberglass cloth that are impregnated with a high-temperature epoxy resin. These layers are then compressed under high pressure and cured to create a solid, dense material that exhibits exceptional mechanical and electrical properties. The result is a material that is incredibly strong, lightweight, and resistant to a wide range of environmental factors.One of the key advantages of G10 material is its excellent electrical insulation properties. This makes it an ideal material for use in electrical and electronic applications, where the material needs to withstand high voltages and frequencies without conducting electricity. In addition to its electrical properties, G10 material also offers excellent mechanical strength and dimensional stability, making it suitable for use in structural and load-bearing applications.{Company} has been able to leverage its expertise in composite materials to develop G10 material that is specifically tailored to meet the unique requirements of its customers. Whether it is for aerospace components, marine equipment, or industrial machinery, {Company} can produce G10 material in a variety of thicknesses, colors, and finishes to meet the specific needs of its customers.The applications for G10 material are vast and diverse. In the aerospace industry, G10 material is used in the production of aircraft components, such as control surfaces, interior panels, and radar equipment. Its lightweight and high-strength properties make it an attractive choice for use in aircraft, where reducing weight is critical for fuel efficiency and performance.In the marine industry, G10 material is used in the construction of boat hulls, decks, and equipment mounts. Its resistance to moisture and chemicals makes it an ideal choice for use in marine environments, where exposure to saltwater and harsh weather conditions can cause traditional materials to degrade over time.In the automotive industry, G10 material is used in the production of high-performance car parts, such as engine components, body panels, and interior trim. Its ability to withstand high temperatures and mechanical stresses makes it a valuable material for use in performance vehicles, where durability and reliability are paramount.In the industrial manufacturing sector, G10 material is used in a variety of applications, such as tooling, fixtures, and machine components. Its high strength and resistance to wear and tear make it an ideal material for use in demanding industrial environments, where traditional materials may fail to provide the required level of performance.With its exceptional properties and versatility, G10 material has become a go-to choice for industries that require high-performance materials. {Company} continues to lead the way in the production of G10 material, offering custom solutions that meet the unique needs of its customers. As the demand for stronger and more durable materials continues to grow, G10 material is likely to play a key role in shaping the future of industrial manufacturing.
How to Easily Install and Maintain SMC Sheet Panels
Title: Groundbreaking Composite Technology Revolutionizing Industrial ProcessesIntroduction:In recent years, significant advancements have been made in the world of materials sciences, leading to transformative developments across various industries. One such breakthrough is the development of Sheet Molding Compound (SMC) technology, a high-performance composite material that has revolutionized industrial processes. This versatile material has gained widespread recognition for its exceptional strength, durability, and exceptional design flexibility. In this article, we will delve into the groundbreaking properties and applications of SMC, as well as explore how it is reshaping industries around the world.1. Overview of SMC:SMC, a composite material made from a combination of resins, fibers, and fillers, has emerged as a game-changer due to its superior mechanical properties. This combination creates a sheet-like material that can be molded into complex shapes, providing manufacturers with unprecedented design possibilities. Moreover, SMC exhibits excellent strength-to-weight ratio, electrical conductivity, and chemical resistance, making it an ideal choice for a wide range of applications.2. Automotive Industry Transformation:The automotive industry, known for its constant pursuit of lightweighting solutions, has embraced SMC as a viable alternative to traditional metals. By incorporating SMC components, vehicles can be substantially lighter, leading to enhanced fuel efficiency and reduced emissions. Additionally, SMC's inherent corrosion resistance contributes to longer vehicle lifespans and reduced maintenance costs. Increasingly, auto manufacturers are adopting SMC in the production of body panels, structural components, and interior parts, revolutionizing the future of mobility.3. Aerospace Applications:The aerospace industry, where lightweight materials are crucial for fuel efficiency and performance, has also been quick to recognize the potential of SMC. By replacing metal parts with SMC components, aircraft can achieve significant weight reductions without compromising integrity or safety. Its exceptional strength and durability also make SMC suitable for critical applications, including aircraft fairings, interior panels, and structural reinforcements. As a result, this technology is contributing to more sustainable and efficient air travel while reducing operating costs.4. Renewable Energy Advancements:The renewable energy sector is another area benefiting from the development of SMC technology. With its excellent resistance to weathering and ultraviolet (UV) radiation, SMC is being used in the construction of wind turbine blades, enabling higher energy production and improved reliability. By using SMC, manufacturers are optimizing blade design for increased efficiency, reducing maintenance requirements, and extending the lifespan of renewable energy infrastructure.5. Infrastructure Reinforcement:The prowess of SMC extends to infrastructure projects as well. In many countries, traditional concrete structures are being supplemented or replaced by SMC-based components. The lightweight nature of SMC makes it a particularly valuable material for retrofitting purposes, where it can reinforce structures without adding excessive weight. Applications include bridge decks, utility poles, and corrosion-resistant structures for coastal areas. This adoption of SMC in the construction sector points toward enhanced durability, efficiency, and sustainability in future infrastructure projects.Conclusion:Sheet Molding Compound (SMC) technology has revolutionized industries through its remarkable mechanical properties and design flexibility. Its applications in the automotive, aerospace, renewable energy, and construction sectors are transforming traditional approaches, prioritizing lightweighting, and enhancing sustainability. As the adoption of SMC continues to grow, we can expect a global shift towards more efficient, durable, and environmentally friendly products and infrastructure.
Essential Guide to High-Quality Electrical Parts: A Resource for Professionals and DIY Enthusiasts
Electrical Parts Company Continues to Innovate and Expand in the Global MarketSince its establishment, Electrical Parts (name removed for confidentiality) has been committed to providing innovative products and solutions to its customers all over the world. With a focus on electrical components and power distribution, Electrical Parts has become one of the major industry players in the global market.Based in the United States, Electrical Parts has developed a robust network of suppliers and customers across the globe, allowing the company to offer a wide range of products and services to meet the diverse needs of its clients. The company has a strong reputation for quality, reliability, and exceptional customer service, which have been key factors in its success.One of the core areas of expertise for Electrical Parts is electrical components. The company offers a broad range of products in this category, including transformers, connectors, wiring devices, and more. These products are designed to meet the high standards of the industry and are tested rigorously to ensure that they are reliable and safe for the end user.In addition to its electrical components, Electrical Parts also specializes in power distribution solutions. The company offers a range of products and services in this area, including switchgear, control panels, and power distribution units. These products are designed to help customers manage their power requirements efficiently and effectively, whether they are looking to power a factory, a data center, or any other type of facility.One of the things that sets Electrical Parts apart from its competitors is its commitment to innovation. The company invests heavily in research and development to ensure that it is always at the forefront of the latest trends and advancements in the industry. By staying ahead of the curve, Electrical Parts is able to provide its customers with cutting-edge solutions that are tailored to their specific needs.Another key factor in Electrical Parts' success is its dedication to customer service. The company operates on a customer-centric model, which means that it always puts the needs of its clients first. From providing personalized solutions to offering prompt and reliable support, Electrical Parts goes above and beyond to ensure that its customers are satisfied with their products and services.Looking to the future, Electrical Parts has ambitious plans for expansion and growth. The company is already established in a number of international markets, but it is looking to expand its reach even further. Through strategic partnerships, acquisitions, and investments, Electrical Parts is aiming to become a truly global player in the industry.At the same time, the company is continuing to innovate and develop new products and solutions that will help its customers meet their evolving needs. With a focus on sustainability and energy efficiency, Electrical Parts is working to create products that are both environmentally friendly and cost-effective.Overall, Electrical Parts has demonstrated its commitment to excellence, innovation, and customer service over the years. With a strong foundation and a clear vision for the future, the company is well-positioned to continue its growth and success in the years to come.
New Halogen-Free G11 Released in China - What You Need to Know
China Halogen Free G11, a leading provider of high-quality electronic materials, has recently announced the launch of a new line of halogen-free G11 laminates. This innovative product is designed to meet the increasing demand for environmentally friendly materials in the electronics industry.The new halogen-free G11 laminates have been developed using cutting-edge technology and rigorous quality control processes. This has allowed China Halogen Free G11 to produce laminates that provide excellent mechanical and electrical properties, while also meeting strict environmental standards. The company has also invested heavily in research and development to ensure that the new laminates offer exceptional performance and reliability.One of the key features of the new halogen-free G11 laminates is their resistance to high temperatures. This makes them ideal for use in a wide range of high-temperature applications, including automotive, aerospace, and industrial electronics. The laminates also offer excellent thermal conductivity, which helps to dissipate heat effectively and maintain the performance of electronic components in demanding environments.In addition to their impressive thermal properties, the halogen-free G11 laminates from China Halogen Free G11 also offer excellent electrical insulation. This makes them suitable for use in high-voltage applications, where reliable insulation is crucial for the safety and performance of electronic systems. The laminates also exhibit low dielectric constant and loss, providing exceptional signal integrity and minimizing signal distortion in high-frequency applications.The environmental benefits of the new halogen-free G11 laminates are also worth noting. By eliminating halogenated compounds from the manufacturing process, China Halogen Free G11 has created a product that is not only safer for the environment but also complies with increasingly stringent regulations on hazardous substances. This makes the laminates an ideal choice for companies looking to reduce their environmental impact and meet the expectations of environmentally conscious consumers."We are delighted to introduce our new line of halogen-free G11 laminates to the market," said a spokesperson for China Halogen Free G11. "These laminates represent the culmination of years of research and development, and we believe they offer a compelling combination of performance, reliability, and environmental responsibility. We are confident that they will prove to be a valuable asset to our customers in the electronics industry."The launch of the new halogen-free G11 laminates is the latest demonstration of China Halogen Free G11's commitment to innovation and excellence in the electronic materials industry. The company's extensive experience and technical expertise have allowed it to develop a range of high-quality products that meet the evolving needs of the market. By consistently investing in research and development, China Halogen Free G11 has been able to stay ahead of the competition and deliver solutions that offer exceptional value to its customers.Moving forward, China Halogen Free G11 is poised to continue pushing the boundaries of what is possible in electronic materials. With a strong focus on sustainability and performance, the company is well-positioned to drive positive change in the industry and provide customers with the materials they need to succeed in an increasingly competitive market.In conclusion, the launch of the new halogen-free G11 laminates from China Halogen Free G11 represents a significant step forward for the electronics industry. By offering a product that combines exceptional performance with environmental responsibility, the company is setting a new standard for electronic materials. As the demand for high-quality, environmentally friendly materials continues to grow, China Halogen Free G11 is well-positioned to meet this demand and help shape the future of the industry.
Fiberglass Reinforced Panels: Durable Wall Options for Your Space
Fiberglass Reinforced Panels: The Perfect Solution for Durable WallsFiberglass Reinforced Panels, also known as FRP panels or simply Fiberglass Panels are the perfect solution for durable walls. These panels are made of a unique combination of fiberglass and resin, resulting in a solid, durable and long-lasting material that is perfect for use in various settings such as residential, commercial and industrial buildings. The panels’ strength and durability make them ideal for use in high-traffic areas, areas with high moisture levels and areas that require easy-to-clean surfaces.One of the leading companies in the supply of fiberglass reinforced panels is the well-known company we shall refer to as “X”. With a track record of providing quality products at affordable prices, X has become a go-to supplier of FRP panels across North America. The company is known for producing high-quality fiberglass reinforced panels that meet or exceed industry standards.Fiberglass reinforced panels come in different sizes and can be used in various settings, including schools, hospitals, prisons, commercial kitchens, and manufacturing plants. The panels are also perfect for use in residential settings, especially in damp areas such as bathrooms and basements. Due to their resistance to moisture and mold, these panels are ideal for use in areas that are prone to water damage.In addition to their durability and strength, fiberglass reinforced panels are easy to install and maintain. They require minimal upkeep beyond basic cleaning and can be easily replaced if damaged. This means that the panels can be used for long periods without the need for frequent repair or replacement.Fiberglass reinforced panels are also cost-effective and eco-friendly. Unlike traditional drywall, they do not require painting, which reduces the cost of installation and maintenance. Additionally, the panels’ longevity and durability mean that they do not need to be replaced as frequently as other materials, reducing waste and saving money on replacement costs.X’s fiberglass reinforced panels are of the highest quality and come in a range of designs and colors, making it easy to find the perfect panels to suit the needs of any project. The company’s panels are designed to meet or exceed industry standards, giving customers the peace of mind that comes from knowing they are using a quality product.In conclusion, fiberglass reinforced panels are the perfect solution for durable walls. They are strong, durable, and easy to install and maintain. X is a leading supplier of fiberglass reinforced panels, providing high-quality panels that meet or exceed industry standards. These panels are perfect for use in various settings, including residential, commercial and industrial buildings and are cost-effective and eco-friendly.
Discover the Benefits and Applications of Insulation Sheets for Effective Temperature Control
[Company Name] Introduces Innovative Insulation Sheet for Enhanced Energy Efficiency[date]In today's rapidly evolving world, energy conservation and environmental sustainability have become paramount concerns. As people increasingly recognize the importance of reducing carbon footprints and conserving energy, industries have responded by developing innovative solutions to enhance energy efficiency. In this regard, [Company Name], a leading provider of cutting-edge insulation products, has recently introduced an exceptional insulation sheet that promises to revolutionize the market.Derived from years of extensive research and development, [Company Name]'s newly launched insulation sheet is designed to address the growing demand for energy-efficient solutions across various sectors. By leveraging advanced materials and cutting-edge technologies, the company strives to provide its customers with a product that not only meets their insulation needs but surpasses expectations.At the core of [Company Name]'s insulation sheet is its exceptional design, incorporating state-of-the-art materials that enable improved thermal performance and energy conservation. Crafted with precision and attention to detail, the insulation sheet offers an unparalleled level of insulation. Its innovative composition allows for enhanced heat resistance, preventing unnecessary energy loss and minimizing energy consumption.The insulation sheet, which is available in various sizes and thicknesses, is incredibly versatile and can be adapted to meet a wide range of insulation requirements. Whether it is residential, commercial, or industrial applications, the sheet seamlessly integrates with diverse structures, ensuring effective thermal insulation and promoting energy efficiency.One of the key highlights of [Company Name]'s insulation sheet is its remarkable resistance to moisture and condensation. This crucial feature ensures that the insulation remains intact over prolonged periods, maintaining its optimum performance. By preventing the formation of moisture on the surface, the insulation sheet not only prolongs its lifespan significantly but also prevents the growth of mold and mildew, creating a healthier and safer environment.In an era characterized by increased awareness of sustainability, the insulation sheet offered by [Company Name] stands out for its commitment to environmental responsibility. The innovative composition of the sheet is free from harmful chemicals, making it an eco-friendly choice for architects, engineers, contractors, and homeowners aiming for sustainable building practices. By embracing this insulation solution, consumers can effectively reduce their energy demands and make a positive impact on the environment.As [Company Name] continues to make strides in the insulation industry, its commitment to quality and customer satisfaction remains unwavering. The company boasts a highly experienced team of professionals dedicated to providing exceptional service and support. With a comprehensive understanding of diverse market requirements, the team collaborates closely with clients to customize insulation solutions and ensure optimal results.Furthermore, [Company Name] has established a robust distribution network to ensure the availability of its insulation sheet nationwide. By strategically partnering with distributors and suppliers, the company aims to make its product easily accessible to customers across different regions.The launch of this innovative insulation sheet by [Company Name] presents an exciting opportunity for companies and individuals seeking to enhance their energy efficiency practices. With its superior thermal performance, resistance to moisture, and commitment to sustainability, this product is set to redefine insulation standards in various industries.As the world continues to grapple with climate change and energy conservation, innovative solutions like [Company Name]'s insulation sheet hold the promise of a more sustainable future. By choosing this groundbreaking product, individuals and organizations can actively contribute to the global effort of reducing energy consumption and mitigating the adverse effects of climate change.About [Company Name]:[Company Name] has been a leading manufacturer and provider of insulation products for over [number] years. With a strong commitment to research and development, the company consistently pushes the boundaries of energy efficiency and sustainability. Offering a wide range of insulation solutions, [Company Name] has earned a reputation for excellence, reliability, and customer satisfaction. For further information, please visit [Company Name]'s official website at [website] or contact their customer service team at [phone number].
Exploring the Benefits and Applications of Epoxy Fiberglass G10
Title: Epoxy Fiberglass G10 Revolutionizes Industrial ApplicationsIntroduction:Innovation and technological advancements continue to shape our world of manufacturing and industrial applications. Among the various groundbreaking materials, Epoxy Fiberglass G10 stands out as a game-changer in its ability to enhance durability, strength, and versatility across numerous industries. This article aims to delve into the key features and applications of Epoxy Fiberglass G10, highlighting its potential to revolutionize traditional manufacturing processes.Unearthing the Potential:Epoxy Fiberglass G10 is a composite material that combines layers of epoxy resin impregnated with woven fiberglass cloth. The resulting material possesses exceptional strength, rigidity, and electrical insulation properties. These attributes make it an ideal choice for applications requiring exceptional mechanical strength, dimensional stability, and reliability.Industrial Applications:1. Electronics and Electrical Components:Epoxy Fiberglass G10 finds significant application in the electronics industry, where it is used extensively in the production of PCBs (Printed Circuit Boards). Its excellent dielectric properties make it an ideal insulator for high-voltage applications. The dimensional stability and exceptional stiffness of Epoxy Fiberglass G10 also contribute towards enhancing the lifespan and performance of electrical components.2. Aerospace and Defense:The aerospace and defense sector relies on materials that can withstand extreme conditions, including high temperatures, impacts, and vibrations. Epoxy Fiberglass G10's remarkable mechanical strength coupled with its resistance to chemical and environmental degradation make it indispensable in the production of structural reinforcements, radomes, antenna assemblies, and advanced insulation systems.3. Automotive Industry:Epoxy Fiberglass G10 contributes significantly to the automotive industry, particularly in the manufacturing of lightweight components. By employing this material in areas such as chassis panels, brackets, and engine components, manufacturers can reduce the overall weight of vehicles without compromising on durability. This, in turn, contributes to improved fuel efficiency and reduced emissions.4. Marine and Offshore Applications:The marine and offshore industries benefit immensely from the exceptional corrosion resistance of Epoxy Fiberglass G10. Its ability to withstand harsh saltwater environments, coupled with its inherent insulation properties, makes it an ideal material for boat hulls, marine electronics, and offshore equipment. Additionally, its excellent moisture resistance ensures prolonged service life in marine applications.Advantages of Epoxy Fiberglass G10:1. High Mechanical Strength: Epoxy Fiberglass G10 exhibits exceptional tensile and flexural strength, making it suitable for various load-bearing applications.2. Dimensional Stability: The material demonstrates minimal expansion or contraction under thermal or mechanical stress, ensuring its longevity.3. Electrical Insulation: Epoxy Fiberglass G10 possesses excellent dielectric properties, making it an effective insulator in electrical and electronic applications.4. Chemical Resistance: The material resists the effects of many chemicals and solvents, making it suitable for versatile applications across different industries.5. Fire Resistance: Epoxy Fiberglass G10 exhibits excellent fire-retardant properties, adding an extra layer of safety to its applications.Company Introduction:At our company, we have capitalized on our expertise and cutting-edge technology to manufacture high-quality Epoxy Fiberglass G10 composites. With a commitment to delivering reliable and durable materials, we have established ourselves as a leading provider in the industry. Our state-of-the-art manufacturing processes ensure stringent quality control, resulting in products that meet the highest industry standards.Conclusion:Epoxy Fiberglass G10 represents a significant leap forward in the world of industrial materials. Its exceptional mechanical strength, electrical insulation, and resistance to various environmental factors make it a material of choice in a plethora of industries. As technology continues to evolve, Epoxy Fiberglass G10 will likely push the boundaries of manufacturing and revolutionize traditional applications, opening doors to new possibilities and innovations.
Simple Methods for Measuring FR-4 Foil Thickness in PCB Manufacturing
When it comes to working with FR-4, one of the most crucial parameters to consider is the thickness of the copper foil on the PCB. However, it is not always easy to determine this parameter, especially if the manufacturer does not readily share this information.Thankfully, there are a few methods that engineers and technicians can use to measure the thickness of the foil on FR-4. Here are some of the most popular options:1. Micrometer: A micrometer is a precision tool used to measure small distances or thicknesses. When measuring the foil thickness on FR-4, a micrometer with a range of 0-1 inch and a resolution of 0.0001 inch can be used to achieve accurate results.2. Cross-Sectioning: Cross-sectioning involves cutting a small slice of the PCB and examining it under a microscope to determine the thickness of the copper layer. Although this technique is more time-consuming and invasive than others, it is also one of the most accurate options available.3. X-ray Fluorescence: X-ray fluorescence (XRF) is a non-destructive method used to analyze the elemental composition of a material. This technique can be used to determine the thickness of copper foil on FR-4 by analyzing the XRF signals from the material. However, XRF equipment can be expensive and may not be accessible to everyone.In addition to these methods, it is important to note that different brands of FR-4 may have slightly different foil thicknesses. Therefore, it is always a good idea to consult the manufacturer's specifications or contact them directly to get accurate information.Overall, while determining the foil thickness on FR-4 may require some effort, the results are well worth it. Knowing this parameter can help ensure the proper functionality and reliability of PCBs in various applications. Keywords: FR-5 sheet, copper foil, thickness, micrometer, cross-sectioning, X-ray fluorescence.